|
................................................................................................................................................................................................................................................ |
˙INTRODUCTION OF MANUFACTURING PROCESS: |
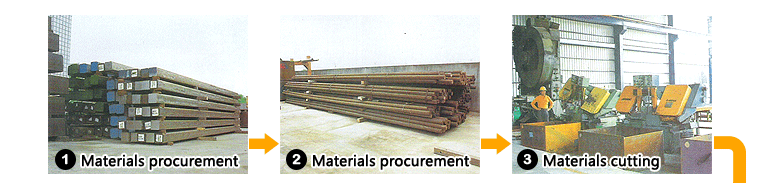 |
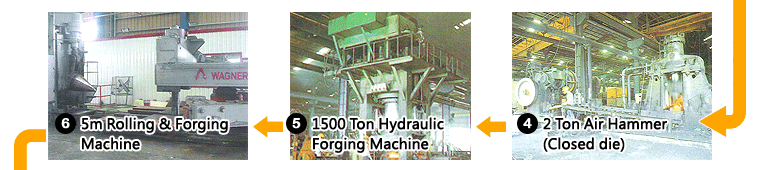 |
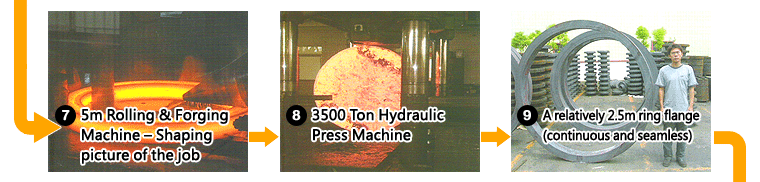 |
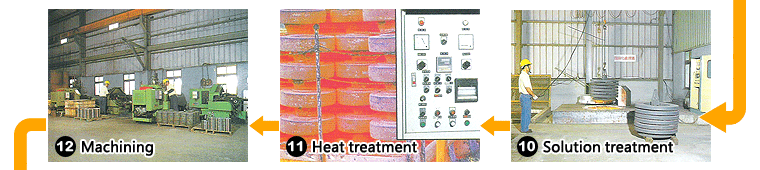 |
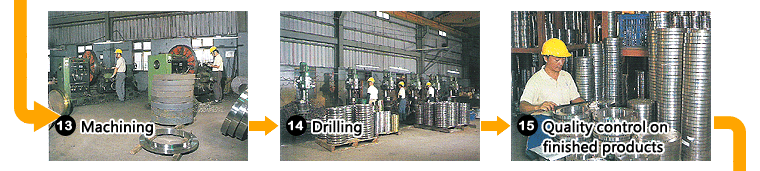 |
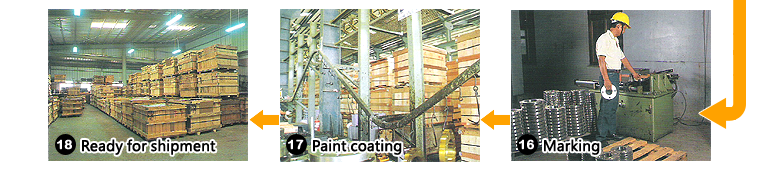 |
|
................................................................................................................................................................................................................................................ |
˙THE FORGING PROCESS FOR LARGE DIAMETER TUBE SHEET.: |
As part of the regular manufacturing process for large diameter tube sheet, forging involves pre-heating, shaping and solution heat treatment. Each workpiece requires a processing time of 5 to 7 days. |
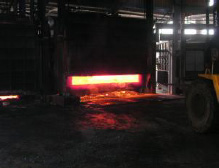
1. First of all, workpiece must be heated
to 1100 ° C to 1180 ° C in a forging
furnace |
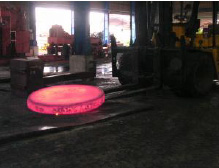
2. Workpiece is removed and ready to
be
further processed |
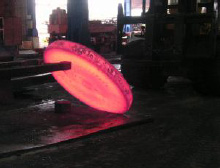
2-1. Workpiece is shaped by hydraulic
press forging |
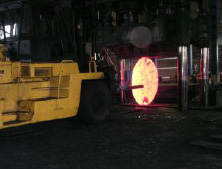
2-2. Press forging works by slowly
applying a continuous pressure or
force onto the workpiece. |
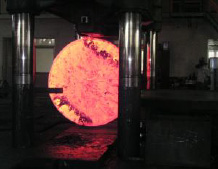
2-3. Workpiece can be deformed
completely, not only the surface, but
also the interior. Press forging can
be used to create the exact size
which is desired. |
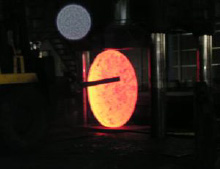
2-4. Due to the constraint of oxidation to
the outer layer of the workpiece, the
level of microcracking of the
finished workpiece is minimized. |
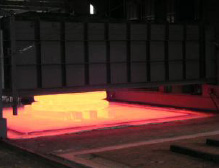
3. Solid solution heat treatment upto
1060 ℃ is applied.
|
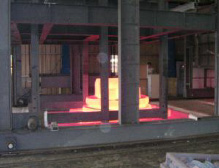
3-1. The heat treatment to be performed
is in accordance with the
requirements specified in the
applicable specification. |
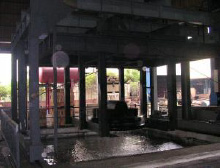
3-2. Lastly, the workpiece will undergo
water cooling and UT inspection,
after solid solution treatment is
finished. |
|
˙FORGING AND SOLUTION TREATMENT: |
What is forging and what is its function? The main concept of forging involves the shaping of workpiece using localized compressive force. |
|
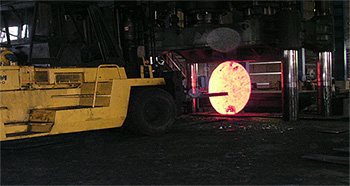
(Press forging such as a hydraulic press machine can produce a blind tube sheet, which is continuous throughout the part, with outside diameter upto 3500mm.) |
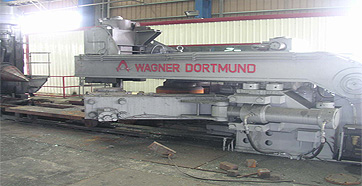
(5 meter roll forging machine can produce a ring flange with outside diameter upto 4500mm) |
Forging uses the idea of hammer and anvil from traditional metalworking process. Forging can produce a piece that is stronger and durable compared to a cast or machined part. During the forging process, the workpiece is shaped, and its internal grain deforms to follow the general shape of the piece. As a result, the grain is continuous throughout the part, giving rise to a piece with improved quality and strength. However, production forging involves significant capital expenditure for equipment, and work hardening tends to occur from forging. Yet, the shape of the workpiece cannot be too complicated.
Forging: a process in which a material, usually metal, is heated and subjected to external compressive forces. It deforms and gives shape to the material. Forging is often classified according to temperature at which it is performed; cold forging and hot forging is widely known and commonly performed. |
|
|
Solution treatment |
|
|
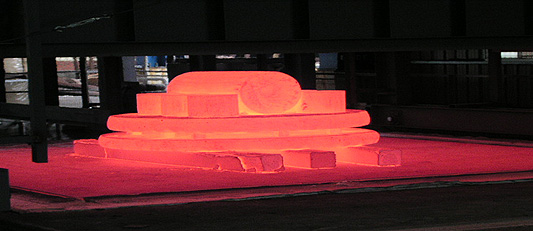
Solution treatment~ the forging furnace is heated to 1040 ℃ or higher(maximum efficacy is up to 1060 ° C) |
|